Viimastel aastatel on laserkeevitus tänu uue energiatööstuse kiirele arengule oma kiirete ja stabiilsete eeliste tõttu kiiresti tunginud kogu uude energiatööstusse. Nende hulgas on laserkeevitusseadmetel suurim kasutusala kogu uues energiatööstuses.
Laserkeevituson oma suure kiiruse, suure sügavuse ja väikese deformatsiooni tõttu muutunud kiiresti esimeseks valikuks kõigil elualadel. punktkeevisõmblustest põkk-keevisõmblusteni, kogumis- ja tihendusõmblusteni,laserkeevitustagab võrratu täpsuse ja kontrolli. See mängib olulist rolli tööstuslikus tootmises ja tootmises, sealhulgas sõjatööstuses, arstiabis, kosmosetööstuses, 3C autoosade, mehaanilise lehtmetalli, uue energia ja muudes tööstusharudes.
Võrreldes teiste keevitustehnoloogiatega on laserkeevitamisel ainulaadsed eelised ja puudused.
Eelis:
1. Kiire kiirus, suur sügavus ja väike deformatsioon.
2. Keevitamist saab teha normaaltemperatuuril või eritingimustes ning keevitusseade on lihtne. Näiteks laserkiir ei triivi elektromagnetväljas. Laserid võivad keevitada vaakumis, õhus või teatud gaasikeskkonnas ning keevitada materjale, mis on läbi klaasi või laserkiirele läbipaistvad.
3. See võib keevitada tulekindlaid materjale, nagu titaan ja kvarts, ning võib keevitada ka erinevaid materjale heade tulemustega.
4. Pärast laseri fokuseerimist on võimsustihedus kõrge. Kuvasuhe võib ulatuda 5:1-ni ja suure võimsusega seadmete keevitamisel kuni 10:1.
5. Võib teostada mikrokeevitust. Pärast laserkiire teravustamist on võimalik saada väike koht ja seda saab täpselt positsioneerida. Seda saab kasutada mikro- ja väikeste detailide kokkupanemisel ja keevitamisel, et saavutada automatiseeritud masstootmine.
6. Sellega saab keevitada raskesti ligipääsetavaid kohti ja teha kontaktivaba pikamaakeevitust suure paindlikkusega. Eriti viimastel aastatel on YAG-i lasertöötlustehnoloogia kasutusele võtnud optilise kiu edastustehnoloogia, mis on võimaldanud laserkeevitustehnoloogiat laiemalt propageerida ja rakendada.
7. Laserkiirt on lihtne ajas ja ruumis poolitada ning mitut kiirt saab töödelda korraga mitmes kohas, mis loob tingimused täpsemaks keevitamiseks.
Defekt:
1. Töödeldava detaili kokkupaneku täpsus peab olema kõrge ja tala asendit toorikul ei saa oluliselt kõrvale kalduda. Selle põhjuseks on asjaolu, et laserpunkti suurus pärast teravustamist on väike ja keevisõmblus kitsas, mistõttu on täitematerjalide lisamine keeruline. Kui tooriku monteerimistäpsus või tala positsioneerimistäpsus ei vasta nõuetele, võivad tekkida keevitusdefektid.
2. Laserite ja nendega seotud süsteemide maksumus on kõrge ning ühekordne investeering on suur.
Levinud laserkeevitusveadliitiumakude valmistamisel
1. Keevitamise poorsus
Levinud defektidlaserkeevituson poorid. Keevitussulavann on sügav ja kitsas. Laserkeevitusprotsessi käigus tungib lämmastik sulabasseini väljastpoolt. Metalli jahutamise ja tahkumise protsessis lämmastiku lahustuvus temperatuuri langedes väheneb. Kui sulametalli metall jahtub ja hakkab kristalliseeruma, langeb lahustuvus järsult ja ootamatult. Sel ajal sadestub suur kogus gaasi, moodustades mullid. Kui mullide ujumiskiirus on väiksem kui metalli kristalliseerumiskiirus, tekivad poorid.
Liitiumpatareide tööstuse rakendustes avastame sageli, et pooride tekkimine on eriti tõenäoline positiivse elektroodi keevitamisel, kuid harva negatiivse elektroodi keevitamisel. Seda seetõttu, et positiivne elektrood on valmistatud alumiiniumist ja negatiivne elektrood on valmistatud vasest. Keevitamise ajal on pinnal olev vedel alumiinium kondenseerunud enne sisemise gaasi täielikku ülevoolu, vältides gaasi ülevoolu ning suurte ja väikeste aukude tekkimist. Väike stomat.
Lisaks eelpool mainitud pooride tekkepõhjustele hõlmavad poorid ka välisõhku, niiskust, pinnaõli jne. Lisaks mõjutab pooride teket ka lämmastiku puhumise suund ja nurk.
Kuidas vähendada keevituspooride teket?
Esiteks, ennekeevitamine, sissetulevate materjalide pinnal olevad õliplekid ja lisandid vajavad õigeaegset puhastamist; liitiumakude tootmisel on sissetuleva materjali kontroll hädavajalik protsess.
Teiseks tuleks kaitsegaasi voolu reguleerida vastavalt sellistele teguritele nagu keevituskiirus, võimsus, asend jne ning see ei tohiks olla liiga suur ega liiga väike. Kaitsekatte rõhku tuleks reguleerida vastavalt sellistele teguritele nagu laseri võimsus ja fookuse asend ning see ei tohiks olla liiga kõrge ega liiga madal. Kaitsekatte otsiku kuju tuleks reguleerida vastavalt keevisõmbluse kujule, suunale ja muudele teguritele, et kaitsekate saaks keevitusala ühtlaselt katta.
Kolmandaks kontrollige töökojas õhu temperatuuri, niiskust ja tolmu. Ümbritseva õhu temperatuur ja niiskus mõjutavad aluspinna ja kaitsegaasi niiskusesisaldust, mis omakorda mõjutab veeauru teket ja väljapääsu sulabasseinis. Kui ümbritseva õhu temperatuur ja niiskus on liiga kõrged, tekib aluspinna ja kaitsegaasi pinnale liiga palju niiskust, mis tekitab suurel hulgal veeauru, mille tulemuseks on poorid. Kui ümbritseva õhu temperatuur ja niiskus on liiga madalad, on aluspinna pinnal ja kaitsegaasis liiga vähe niiskust, mis vähendab veeauru teket, vähendades seeläbi poore; laske kvaliteedipersonalil tuvastada keevitusjaama temperatuuri, niiskuse ja tolmu sihtväärtus.
Neljandaks kasutatakse laserkiigutamise meetodit pooride vähendamiseks või kõrvaldamiseks lasersügavkeevitusel. Keevitamisel lisanduva õõtsumise tõttu põhjustab tala edasi-tagasi liikumine keevisõmblusele osa keevisõmbluse korduva ümbersulamise, mis pikendab vedela metalli viibimisaega keevitusvannis. Samal ajal suurendab tala läbipaine ka soojuse sisendit pinnaühiku kohta. Keevisõmbluse sügavuse ja laiuse suhe väheneb, mis soodustab mullide teket, kõrvaldades seeläbi poorid. Teisest küljest paneb tala kõikumine väikese augu vastavalt õõtsuma, mis võib anda ka keevitusvannile segamisjõu, suurendada keevitusvanni konvektsiooni ja segamist ning avaldada kasulikku mõju pooride eemaldamisele.
Viiendaks, impulsi sagedus, impulsi sagedus viitab laserkiire kiiratavate impulsside arvule ajaühikus, mis mõjutab soojuse sisendit ja soojuse akumuleerumist sulabasseinis ning seejärel temperatuurivälja ja vooluvälja sulas. bassein. Kui impulsi sagedus on liiga kõrge, põhjustab see sulabasseini liigset soojust, mis põhjustab sulabasseini liiga kõrge temperatuuri, tekitades metalliauru või muid elemente, mis on kõrgel temperatuuril lenduvad, mille tulemuseks on pooride teke. Kui impulsi sagedus on liiga madal, põhjustab see ebapiisava soojuse akumuleerumist sulabasseinis, mis põhjustab sulabasseini liiga madala temperatuuri, mis vähendab gaasi lahustumist ja väljavoolu, mille tulemuseks on pooride teke. Üldiselt tuleks impulsi sagedus valida mõistlikus vahemikus, lähtudes substraadi paksusest ja laseri võimsusest, ning vältida seda, et see oleks liiga kõrge või liiga madal.
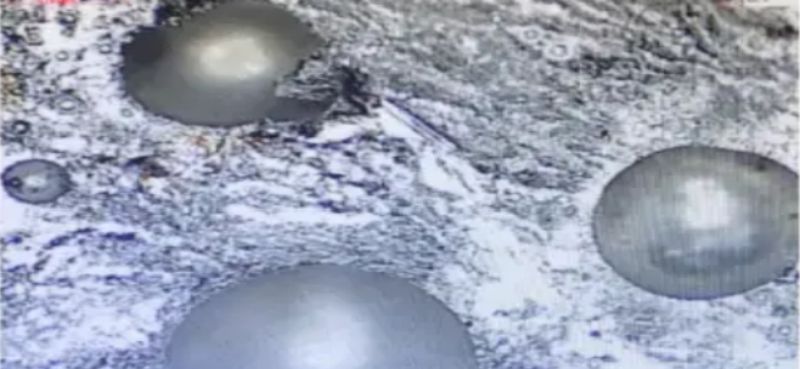
Aukude keevitamine (laserkeevitus)
2. Keevispritsmed
Keevitusprotsessi ja laserkeevituse käigus tekkivad pritsmed mõjutavad tõsiselt keevisõmbluse pinna kvaliteeti ning saastavad ja kahjustavad objektiivi. Üldine jõudlus on järgmine: pärast laserkeevituse lõpetamist ilmuvad materjali või tooriku pinnale palju metalliosakesi, mis kleepuvad materjali või tooriku pinnale. Kõige intuitiivsem jõudlus seisneb selles, et galvanomeetri režiimis keevitamisel tekivad pärast galvanomeetri kaitseläätse teatud kasutusperioodi pinnale tihedad lohud ja need on tekkinud keevituspritsmetest. Pärast pikka aega on valgust lihtne blokeerida ja keevitusvalgustiga on probleeme, mille tulemuseks on rida probleeme, nagu keevitus katkes ja virtuaalne keevitamine.
Mis on pritsimise põhjused?
Esiteks, võimsustihedus, mida suurem on võimsustihedus, seda lihtsam on pritsmeid tekitada ja pritsmed on otseselt seotud võimsustihedusega. See on sajandivanune probleem. Vähemalt seni ei ole tööstus pritsmeprobleemi suutnud lahendada ja võib vaid öelda, et seda on veidi vähendatud. Liitiumakutööstuses on pritsimine aku lühise suurim süüdlane, kuid selle algpõhjust pole õnnestunud lahendada. Pritsmete mõju akule saab vähendada ainult kaitse seisukohalt. Näiteks on keevitusosa ümber lisatud ring tolmueemaldusporte ja kaitsekatteid ning ringidena õhknugade read, et vältida pritsmete mõju või isegi aku kahjustamist. Võib öelda, et keevitusjaama ümbruse keskkonna, toodete ja komponentide hävitamine on ammendanud vahendid.
Pritsmeprobleemi lahendamise kohta võib vaid öelda, et keevitusenergia vähendamine aitab pritsmeid vähendada. Ebapiisava läbitungimise korral võib abi olla ka keevituskiiruse vähendamisest. Kuid mõne protsessi erinõuete puhul on sellel vähe mõju. See on sama protsess, erinevatel masinatel ja erinevatel materjalide partiidel on täiesti erinevad keevitusefektid. Seetõttu kehtib uues energiatööstuses kirjutamata reegel, ühe seadme jaoks üks komplekt keevitusparameetreid.
Teiseks, kui töödeldud materjali või tooriku pinda ei puhastata, põhjustavad tõsiseid pritsmeid ka õliplekid või saasteained. Sel ajal on kõige lihtsam puhastada töödeldud materjali pind.
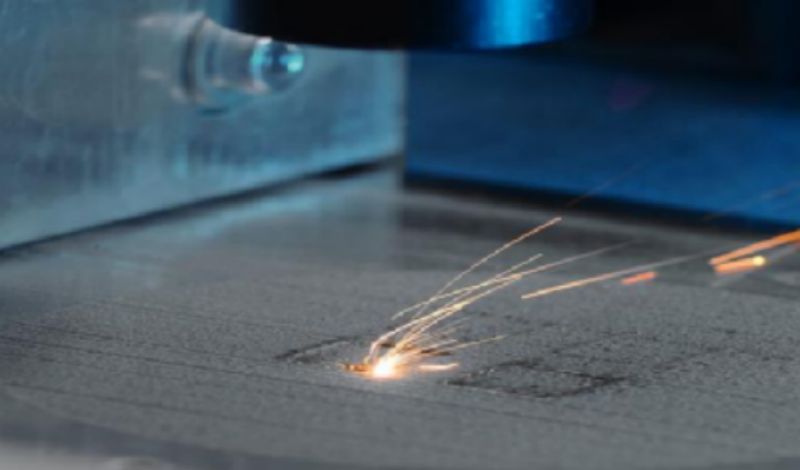
3. Laserkeevituse kõrge peegeldusvõime
Üldiselt tähendab kõrge peegeldus tõsiasja, et töötlemismaterjalil on väike eritakistus, suhteliselt sile pind ja madal neeldumiskiirus lähi-infrapuna laserite puhul, mis toob kaasa suure laseremissiooni ja kuna kasutatakse enamikku lasereid. vertikaalselt Materjali või väikese kalde tõttu siseneb tagasipöörduv laservalgus uuesti väljundpeasse ja isegi osa tagasitulevast valgusest ühendatakse energiat edastavasse kiudu ja kandub mööda kiudu tagasi sisemusse laseri sees olevad põhikomponendid on jätkuvalt kõrgel temperatuuril.
Kui laserkeevitamise ajal on peegeldusvõime liiga kõrge, võib kasutada järgmisi lahendusi:
3.1 Kasutage peegeldusvastast katet või töödelge materjali pinda: keevitusmaterjali pinna katmine peegeldusvastase kattega võib tõhusalt vähendada laseri peegeldusvõimet. See kate on tavaliselt madala peegeldusvõimega spetsiaalne optiline materjal, mis neelab laserenergiat, mitte ei peegelda seda tagasi. Mõnes protsessis, nagu voolukollektori keevitamine, pehme ühendamine jne, võib pinnale olla ka reljeef.
3.2 Keevitusnurga reguleerimine: Keevitusnurga reguleerimisega saab laserkiire langeda keevitusmaterjalile sobivama nurga all ja vähendada peegeldust. Tavaliselt on peegelduste vähendamiseks hea viis laserkiire langemine keevitatava materjali pinnaga risti.
3.3 Lisaabsorbendi lisamine: keevitusprotsessi ajal lisatakse keevisõmblusele teatud kogus lisaabsorbenti, näiteks pulbrit või vedelikku. Need absorbendid neelavad laserenergiat ja vähendavad peegelduvust. Sobiv absorbent tuleb valida konkreetsete keevitusmaterjalide ja kasutusstsenaariumide põhjal. Liitiumakutööstuses on see ebatõenäoline.
3.4 Kasutage laseri edastamiseks optilist kiudu: võimalusel võib peegelduvuse vähendamiseks kasutada optilist kiudu laseri keevitusasendisse edastamiseks. Optilised kiud võivad juhtida laserkiire keevitusalale, et vältida otsest kokkupuudet keevitusmaterjali pinnaga ja vähendada peegelduste teket.
3.5 Laseri parameetrite reguleerimine: reguleerides selliseid parameetreid nagu laseri võimsus, fookuskaugus ja fookuse läbimõõt, saab laserenergia jaotust juhtida ja peegeldusi vähendada. Mõne peegeldava materjali puhul võib laservõimsuse vähendamine olla tõhus viis peegelduste vähendamiseks.
3.6 Kasutage kiire jaoturit: kiirjaotur võib suunata osa laserenergiast neeldumisseadmesse, vähendades sellega peegelduste esinemist. Kiirjagamisseadmed koosnevad tavaliselt optilistest komponentidest ja neeldujatest ning sobivate komponentide valiku ja seadme paigutuse kohandamisega on võimalik saavutada väiksem peegeldusvõime.
4. Keevitamise allalõige
Millised protsessid põhjustavad liitiumaku tootmisprotsessis tõenäolisemalt hinna allalöömist? Miks tekib allahindlus? Analüüsime seda.
Alalõigatud, üldiselt ei ole keevitusmaterjalid omavahel hästi ühendatud, vahe on liiga suur või soon on nähtav, sügavus ja laius on põhimõtteliselt suuremad kui 0,5 mm, kogupikkus on suurem kui 10% keevisõmbluse pikkusest või tooteprotsessi standardist suurem nõutud pikkus.
Kogu liitiumaku tootmisprotsessis on allalõige tõenäolisem ja see jaotub tavaliselt silindrilise katteplaadi tihendamise eelkeevitamisel ja keevitamisel ning ruudukujulise alumiiniumkesta katteplaadi tihendamise eelkeevitamisel ja keevitamisel. Peamine põhjus on see, et tihenduskatteplaat peab keevitamiseks kestaga koostööd tegema, tihenduskatteplaadi ja kesta vahelise sobitamise protsessis võivad tekkida liigsed keevislõhed, sooned, kokkuvarisemine jne, mistõttu on see eriti altid sisselõigetele. .
Mis siis põhjustab allahindlust?
Kui keevituskiirus on liiga suur, ei ole keevisõmbluse keskpunkti suunatud väikese augu taga vedelal metallil aega ümber jaotuda, mille tulemuseks on keevisõmbluse tahkumine ja läbilõikamine mõlemal pool. Ülaltoodud olukorda silmas pidades peame optimeerima keevitusparameetreid. Lihtsamalt öeldes on see korduvad katsed erinevate parameetrite kontrollimiseks ja jätkatakse DOE tegemist, kuni sobivad parameetrid on leitud.
2. Keevitusmaterjalide liigsed keevisvahed, sooned, varingud jne vähendavad tühimikke täitva sulametalli kogust, muutes sisselõigete tekkimise tõenäolisemaks. See on seadmete ja tooraine küsimus. Kas keevitusmaterjalid vastavad meie protsessi sissetulevatele materjalidele, kas seadmete täpsus vastab nõuetele jne. Tavapraktika on pidev tarnijate ja seadmete eest vastutavate inimeste piinamine ja peksmine.
3. Kui energia langeb laserkeevituse lõpus liiga kiiresti, võib väike auk kokku kukkuda, mille tulemuseks on lokaalne allalõige. Võimsuse ja kiiruse õige sobitamine võib tõhusalt ära hoida allalõigete teket. Nagu vanasõna ütleb, korrake katseid, kontrollige erinevaid parameetreid ja jätkake DOE-d, kuni leiate õiged parameetrid.
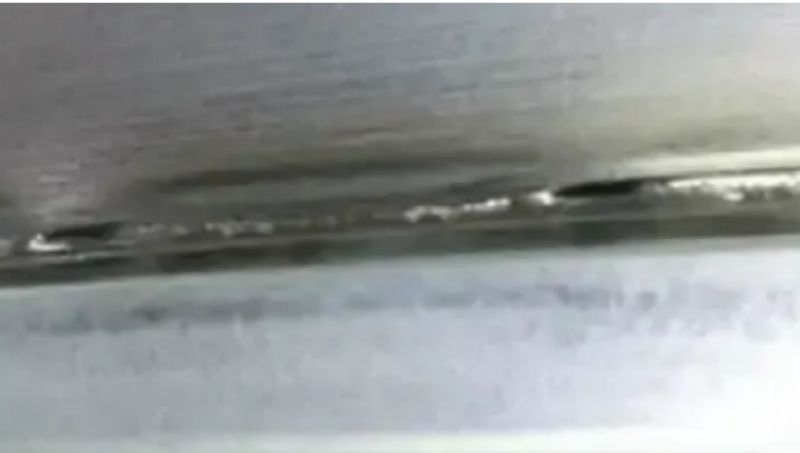
5. Keevituskeskuse kokkuvarisemine
Kui keevituskiirus on aeglane, on sulavann suurem ja laiem, mis suurendab sulametalli kogust. See võib muuta pindpinevuse säilitamise keeruliseks. Kui sulametall muutub liiga raskeks, võib keevisõmbluse keskpunkt vajuda ning moodustada lohke ja süvendeid. Sel juhul tuleb energiatihedust vastavalt vähendada, et vältida sulamisbasseini kokkuvarisemist.
Teises olukorras moodustab keevituspilu lihtsalt kokkuvarisemist, põhjustamata perforatsiooni. See on kahtlemata seadmete pressi sobivuse probleem.
Laserkeevitamisel tekkida võivate defektide ja erinevate defektide põhjuste nõuetekohane mõistmine võimaldab sihipärasemat lähenemist ebanormaalsete keevitusprobleemide lahendamiseks.
6. Keevispraod
Pideva laserkeevituse käigus tekkivad praod on peamiselt termilised praod, näiteks kristallpraod ja veeldumispraod. Nende pragude peamine põhjus on keevisõmbluse tekitatud suured kokkutõmbumisjõud enne selle täielikku tahkumist.
Laserkeevituse pragude tekkimisel on ka järgmised põhjused:
1. Põhjendamatu keevisõmbluse konstruktsioon: keevisõmbluse geomeetria ja suuruse vale projekteerimine võib põhjustada keevituspinge kontsentratsiooni, põhjustades seeläbi pragusid. Lahenduseks on keevisõmbluse konstruktsiooni optimeerimine, et vältida keevituspinge kontsentratsiooni. Saate kasutada sobivaid nihkekeevisõmblusi, muuta keevisõmbluse kuju jne.
2. Keevitusparameetrite mittevastavus: keevitusparameetrite ebaõige valik, nagu liiga kiire keevituskiirus, liiga suur võimsus jne, võib põhjustada keevituspiirkonnas ebaühtlaseid temperatuurimuutusi, mille tagajärjeks on suur keevituspinge ja praod. Lahenduseks on keevitusparameetrite reguleerimine, et need vastaksid konkreetsele materjalile ja keevitustingimustele.
3. Keevituspinna halb ettevalmistus: keevituspinna korralik puhastamata jätmine ja eeltöötlemata jätmine enne keevitamist, näiteks oksiidide, rasvade jms eemaldamine, mõjutab keevisõmbluse kvaliteeti ja tugevust ning põhjustab kergesti pragude tekkimist. Lahenduseks on keevituspinna piisav puhastamine ja eeltöötlemine, et tagada keevitusalal olevate lisandite ja saasteainete tõhus töötlemine.
4. Keevitussoojussisendi ebaõige juhtimine: Soojussisendi halb juhtimine keevitamise ajal, näiteks liigne temperatuur keevitamise ajal, keevituskihi ebaõige jahutuskiirus jne, põhjustab keevitusala struktuuri muutusi, mille tulemuseks on pragude tekkimine. . Lahenduseks on temperatuuri ja jahutuskiiruse reguleerimine keevitamise ajal, et vältida ülekuumenemist ja kiiret jahtumist.
5. Ebapiisav pingeleevendus: ebapiisav pingevabastustöötlus pärast keevitamist põhjustab keevitatud ala ebapiisava pingevabastuse, mis põhjustab kergesti pragude tekkimist. Lahenduseks on keevitamise järgselt sobiva pingeleevendustöötluse läbiviimine, näiteks kuumtöötlus või vibratsioonitöötlus (peamine põhjus).
Mis puutub liitiumakude tootmisprotsessi, siis millised protsessid põhjustavad tõenäolisemalt pragusid?
Üldjuhul tekivad tihenduskeevituse ajal praod, nt silindriliste teraskestade või alumiiniumkestade tihenduskeevitamisel, ruudukujuliste alumiiniumkestade tihenduskeevitamisel jne. Lisaks on mooduli pakkimise käigus kalduvus ka voolukollektori keevitamisele. pragudeni.
Loomulikult saame nende pragude vähendamiseks või kõrvaldamiseks kasutada ka täitetraati, eelsoojendust või muid meetodeid.
Postitusaeg: 01.09.2023